De missie van Maria: van Additive Manufacturing een standaard productieroute maken
Voor elke toepassing – nieuw of bestaand – in de luchtvaart geldt: het moet lichter, kostenefficiënter en minder belastend voor het klimaat. Ondanks de opkomst van composieten, zullen metalen ook in de nieuwe generatie vliegtuigen een onmisbaar onderdeel zijn. Voor additive manufacturing (AM) is daarin een belangrijke rol weggelegd. Deze technologie is bij uitstek goed in het combineren van verschillende materialen om optimale combinaties van eigenschappen te creëren, maar dan op een meer efficiënte en duurzame manier.
Die combinaties van microstructuren en samenstellingen is precies waar Maria Montero-Sistiaga zich als R&D engineer bij het Koninklijk Nederlands Lucht- en Ruimtevaartcentrum (NLR) mee bezighoudt. Het is inmiddels bijna vier jaar geleden dat ze bij NLR begon in 2019, het “voelt alsof de tijd voorbij gevlogen is.” Toch wist ze in die relatief korte periode al veel klaar te spelen. Drie publicaties, een keynote op een van de belangrijkste additive manufacturing (AM) events ter wereld en een paper dat geselecteerd werd voor een andere toonaangevende AM conferentie, om maar wat te noemen.
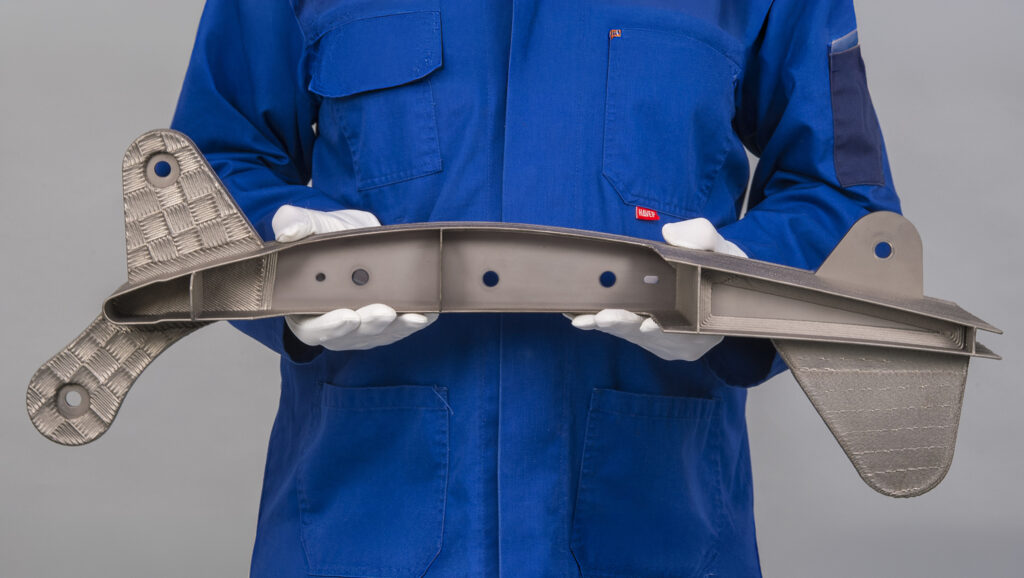
Een eindeloze fascinatie voor materialen
Haar fascinatie voor materialen begint in de werkplaats van haar vader, in een klein dorpje in het Spaanse Baskenland. “Mijn vader, broers en zussen waren altijd wel iets aan het sleutelen, repareren of frezen. Als jong meisje vond ik alles wat mijn broers deden interessant, dus ik heb vele uren achter die werkbank doorgebracht.”
Zo komt het dat ze op haar achttiende begint met een bachelor industrieel design aan de Mondragan Universiteit. Bij het vak Materials is het liefde op het eerste gezicht. “Ik dacht meteen: dit is het. De eerste keer dat ik materialen van dichtbij bestudeerde, ging er een wereld voor me open. Al die microstructuren waarvan de samenstelling bepaalt hoe een materiaal zich gaat gedragen; het fascineert me mateloos. Als je op die manier naar objecten kijkt, wordt zelfs een tafel interessant.”
Drie jaar later vertrekt ze naar België, waar ze aan de KU Leuven een master en later ook haar doctorstitel haalt – met in beide een hoofdrol voor materialen. Ze specialiseert zich in additive manufacturing. “Eigenlijk zou ik maar voor een jaar naar België gaan, maar twaalf jaar later woon ik nog steeds in de Benelux”, lacht Maria.
“Een laagje crème, een laagje deeg, een laagje chocolade, dan weer een laagje deeg. Met 3D-printen doen we eigenlijk hetzelfde”
3D-printen: een duurzame taart voor de luchtvaart
Bij het Metal Additive Manufacturing Technology Centre (MAMTeC) van NLR houdt Maria zich bezig met het ontwikkelen van AM-technologieën om vliegtoestellen te verduurzamen en verbeteren. Ze vergelijkt haar werk met het bakken van een taart. “Een laagje crème, een laagje deeg, een laagje chocolade, dan weer een laagje deeg. Met 3D-printen doen we hetzelfde. Ik kijk zowel naar de ingrediënten van de taart – meer of minder suiker – als de omstandigheden waarin we de taart bakken – de temperatuur van de oven.”
Deze hightech taart kan de luchtvaart een behoorlijk stuk duurzamer maken. Een voorbeeld daarvan, is laser powder directed energy desposition (LP-DED). Hierbij wordt het materiaal vanuit een ‘nozzle’ – een klein pijpje – op een robotarm of meerassige machine toegevoegd aan een bestaand oppervlak en vervolgens gesmolten door een laser. MAMTeC produceerde eerder dit jaar een flaperon rib op ware grootte met deze technologie. Een flaperon is een stuurvlak van een vliegtuig dat zowel de functie van flap als rolroer vervult.
“Een flaperon rib is groot, lang en dun: voor ons de ideale testcase. LP-DED is heel interessant voor de productie van complexe, grote onderdelen”, legt Maria uit. “De productiesnelheid ligt hoog en de productie is zuiniger dan bij andere AM-technologieën. Nu worden onderdelen als een flaperon vaak nog uit massieve blokken gefreesd, wat veel afval oplevert tijdens het productieproces. Ons doel met dit onderzoek was om de hele productieketen – van procesoptimalisatie tot productie en nabewerking – te laten zien voor de productie van een titanium flaperon rib. Ik ben er trots op dat dat ons gelukt is.”
Uitdagend werk met veel afwisseling
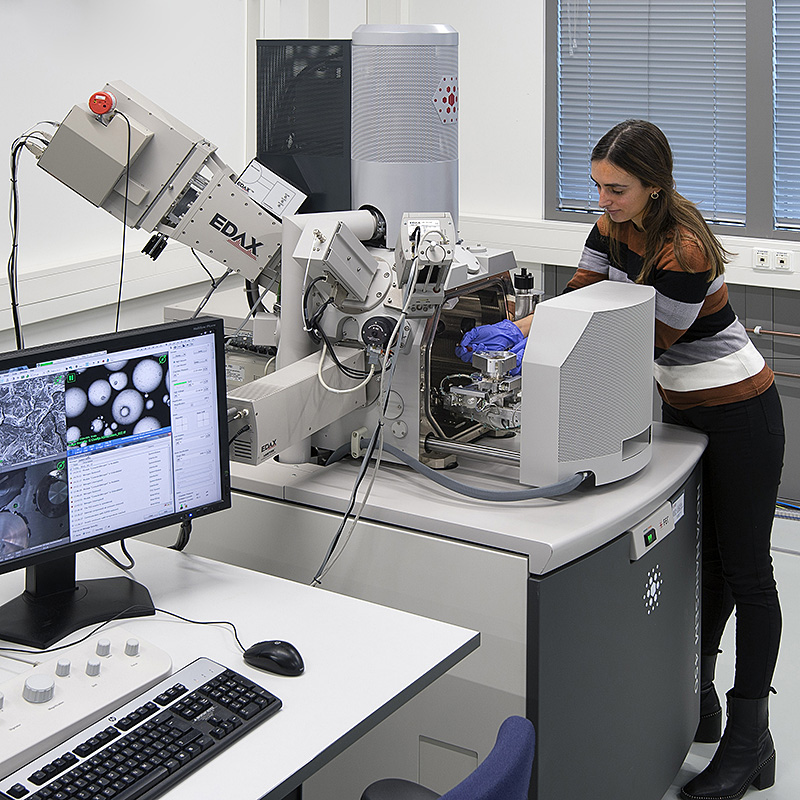
Tijdens het gesprek wordt een ding steeds opnieuw duidelijk: Maria heeft een grote passie voor het werk dat ze doet. “Mijn baan is elke dag anders, ik leer elke dag nieuwe dingen. AM is een heel veelzijdig werkveld waar veel disciplines, zoals mechanica, statistiek, digitalisatie, en engineering, bij komen kijken. Daarnaast ben je als R&D Engineer zowel bezig met de technologie, als met de projectmatige kant. Het ene moment schrijf ik subsidieaanvragen, het andere moment sta ik met collega’s op het laboratorium. Die afwisseling vind ik geweldig.”
De hype voorbij
AM is bezig aan een gestage opmars binnen de luchtvaartsector. “We zijn de hype inmiddels wel voorbij. Bijna alle bedrijven waarmee we samenwerken zien in dat bijvoorbeeld 3D-printen veel voordelen heeft. De grootste uitdaging is om het vertrouwen van de industrie te winnen. De sector is voor een groot deel verantwoordelijk voor de certificerings- en kwaliteitsprocessen. Met name in de luchtvaart zijn veiligheidseisen, logischerwijs, heel hoog. Dat zorgt ervoor dat het lang duurt voordat nieuwe technologieën toegepast mogen worden.”
Om dit proces te versnellen, werkt Maria namens NLR aan het opstellen van nieuwe virtuele kwalificatie- en certificeringsprocessen voor AM. “Nu worden onderdelen beoordeeld op een vast ontwerp, vaste parameters en platformconfiguratie. Als we een kleine wijziging aanbrengen in het ontwerp, moet het hele kwalificatieproces weer van vooraf aan beginnen. Door dit proces te digitaliseren en vernieuwen hopen we dat dit in de toekomst sneller kan.”
Daarnaast is het belangrijk om onderzoek te blijven doen, te blijven aantonen: AM is veilig, flexibel en duurzamer dan traditionele productieprocessen. “Mijn carrière en de opkomst van 3D-printen van metalen zijn ongeveer tegelijkertijd begonnen. Twaalf jaar geleden wist nog bijna niemand van AM af, een enorm verschil met nu. Ik zie het echt als mijn missie om van AM een standaard productieroute te maken voor de luchtvaart.”