The challenge
In recent years, improving energy efficiency (i.e. fuel consumption) and emission reduction have led to increased engine sizes and bypass ratios. These modifications create a crucial noise issue due to the emission of low-frequency noise and the size and effectiveness limitations of the current noise-absorbing structures (liners).
The solution
This project explored innovative ideas and concepts for efficient noise reduction by novel liner concepts. In addition, it investigated the potential of dissipative surfaces as encountered with the development of meta-materials. AM was studied as a potential solution for producing more efficient noise-reduction liners. Several concepts have been addressed to aim for low-frequency and broad-spectrum absorption. AM opens up new possibilities for manufacturing complicated structures for noise absorbers which have not been technically and/or economically possible before.
What did we do?
At NLR-MAMTeC, various acoustic liner prototypes were manufactured with LPBF that were designed by the Institute of Sound and Vibration Research (ISVR). The designs are characterised by the different angled features and hole sizes. The main criterion for the AM part was repeatable quality of the acoustic liners’ performance and controllable size of the holes. The liner prototypes were
tested in the impedance tube at the Vertical Flight and Aeroacoustics department at NLR. The manufactured liners’ performance is in line with the model predictions, although some modifications had to be made to the hole diameters due to the variation between the jobs.
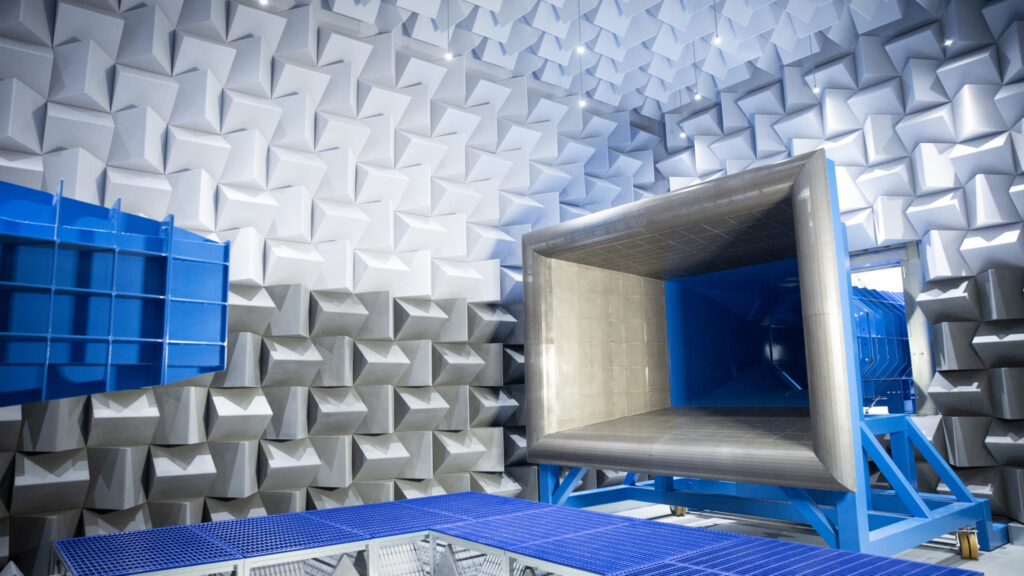
Project partners:
DLR (project lead), Royal NLR, AEDS, Airbus, Cira, CNRS, CMOTI, DASSAV, ECL, EPFL, EMPA, INCAS, Onera, PVS, Polls-Royce, Safran, Southampton U., TsAGI, TUBS, TU Delft, U Bristol, UCP, U Roma Tre, VKI
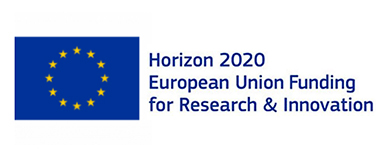
The ARTEM project has received funding from the European Union’s Horizon 2020 research and innovation program (Future Sky EREA initiative).