In the autumn of 2019, NLR flew the HYDRA-1 drone powered by hydrogen gas. The enhanced successor, HYDRA-2, is now ready. Like its smaller predecessor, this drone is currently equipped with a commercially available, composite hydrogen gas tank,. However, if hydrogen fuel could be carried in liquid form, the endurance of the drone would be increased considerably.
Metal fatigue
At present, liquid hydrogen storage tanks, used in spacecraft, are made wholly of metal or of metal-lined composites. In space applications, these tanks are only designed to be single use. Consequently, the metal parts of the hydrogen tanks were never designed to be resistant to a common problem in metal components: fatigue, a critical design criterion for aircraft structures.
Metal fatigue occurs when a metal object bends up and down for long enough – this need not, in fact, be all that many times – so that in the long term a small defect or crack can grow to become a fracture. Apart from saving weight, this is an important reason for switching to the use of composite materials. The solution is to construct the tanks from composite materials, which have the double benefit of not suffering from metal fatigue and saving weight.
Major ambition
Combining liquid hydrogen as an energy carrier and tanks made entirely of composite materials raises complex issues. According to Bert Thuis, departmental manager for Structures Technology. ‘This calls for the use of different forms of technical expertise from several different NLR departments and we are also seeing partnerships with external parties’, he says. ‘We are going to investigate how we can redesign and modify the existing commercial system and make it suitable for liquid hydrogen. We are assuming storage at extremely low temperatures here (-263℃ and relatively low pressures (1 to 4 bar)). We will then build and test a prototype of this. We will also reassess the existing HYDRA powertrain and may modify it. But it should be borne in mind that fuelling with liquid hydrogen cannot yet be taken for granted. That requires adjustments for the necessary infrastructure.’
When the new systems are integrated in the drone, test flights can take place. ‘And don’t forget the certification and the regulations’, Thuis emphasises. ‘These always remain very important for conducting the preparations and flights with the drone safely.’
NLR aims to make a first flight with the HYDRA-2 using a hybrid metal-composite tank in December 2021. This will be followed by flights using a liquid hydrogen tank made entirely of composite materials by December 2022 at the latest.
More information
please contact Bert Thuis (bert.thuis@nlr.nl).
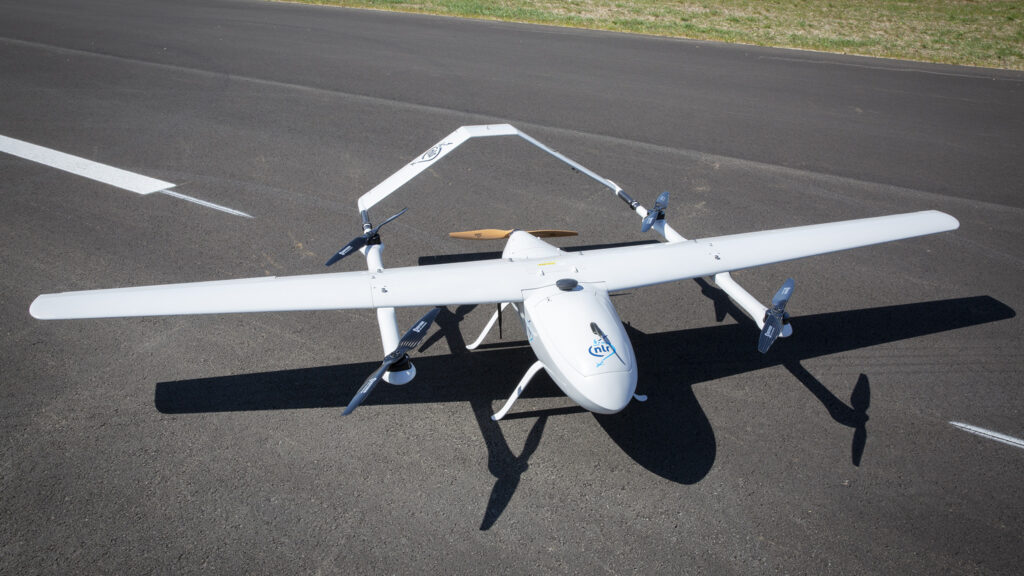