NLR develops advanced services supporting more complex operations in dense areas such as assistance for Detect & Avoid and U-space Weather Information Services. To provide drone operators with information about the actual and forecasted weather situation, NLR develops a service to provide hyperlocal wind nowcasting for drones by drones. Due to their light-weight nature, small drones can be vulnerable to wind. This is particularly true for low altitude operations in urban areas where both wind speed and direction can change abruptly. To safely realize numerous applications of drones in urban areas, real-time and accurate knowledge of low altitude winds is needed. To develop this service NLR executed the METSIS project (METeo Sensors In the Sky)
The challenge
The goal of the METSIS concept is to estimate and communicate hyperlocal wind information to drone operators in real time using data measured by the drones themselves, i.e., by using drones as an aerial wind sensor network. The novelty of the METSIS concept is that a network of drones are being used to not only measure the wind states at the locations of the drones themselves, but to estimate the 3D wind field within the area encompassing the wind measurements using the Meteo-Particle Model (MPM). The resulting wind field estimates, which are updated when new measurements are received from individual drones, can be used by drone operators for numerous applications, including for the computation of wind optimized routes to improve mission safety and efficiency (i.e., battery life/range).
The solution
The MENSIS concept consists of three main steps:
- Airborne drones measure instantaneous wind states and transmit data to a ground station.
- Ground station uses the Meteo Particle Model (MPM) to estimate the wind field in real time.
- The ground station communicates wind field data to drone operators via the U-space weather information service.
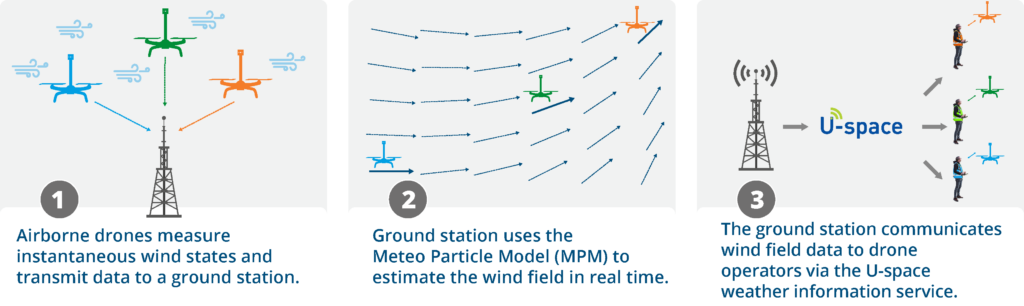
What did we do?
Royal NLR performed a proof-of-concept experiment using four drones to determine the feasibility and accuracy of the concept at low altitudes. For the experiment, ultrasonic anemometers were mounted to each drone to measure local winds. The calibration of the wind sensors was tested using the NLR Anechoic Wind Tunnel. Subsequently, flight-tests were performed at the NLR Drone Centre to evaluate the effect of obstacles, drone motion, measurement density,
and measurement errors on concept accuracy. Wind fields estimated during the flight-tests were published to the AirHub Drone Operations Center (DOC) system to demonstrate the communication of this data to U-space end-users in real-time. The results indicated that the METSIS concept is a promising solution for the wind nowcast component of the U-space weather information service.
Project partners:
Industry: Airhub
Research organisations: Royal NLR
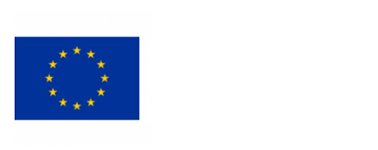
METSIS is co-funded by the European Union. This message doesn’t necessarily reflect the views of the EU.