Hydrogen has been identified as a key priority to achieve the European Green Deal for a sustainable economy. By converting the construction of the hydrogen tank from existing metallic solutions to composites, the liquid hydrogen (LH2) composite tank will achieve weight savings that enable the advancement of liquid hydrogen as a sustainable fuel source for civil aviation. This will lower the carbon footprint of air travel and extend the flight range of aircraft by reducing construction weight and cost.
The challenge
For single-aisle commercial aircraft, the energy density of compressed hydrogen gas is not sufficient to provide the necessary range; this can only be reached with liquid hydrogen, stored at 20 Kelvin/-253 °C. The project aims to develop a linerless long-life lightweight composite tank that can withstand the low temperature of liquid hydrogen and related thermal stress.
The solution
The project will focus on the application of microcrack-resistant composite materials with sufficiently low permeability for hydrogen. In order to comply with boil-off and dormancy requirements without adding significant weight and/or volume, a vacuum/MLI insulated tank will be developed with contributions of all consortium members. The tank will be equipped with fluid level sensors and sensors for safety systems. During the design phase, digital design strategies will be used to minimise thermal stress and optimize utilisation of automated manufacturing technologies.
What did we do?
LR has developed additional facilities for testing composite materials at 20 Kelvin. Several semi-crystalline thermoplastic composites (Toray) have been screened regarding their properties at this very low temperature. Screening of some thermoset composite materials from Toray will follow shortly. The materials are also characterised regarding their permeability properties and resistance against thermal cycling
down to 4 Kelvin. Together with project partners, a suitable composite material will be selected and characterised regarding engineering properties at 20 Kelvin. Next a small scale vacuum insulated tank of approximately 70 liters will be developed and tested regarding mechanical and thermal performance. Durability will be tested by repeated filling and extraction of hydrogen.
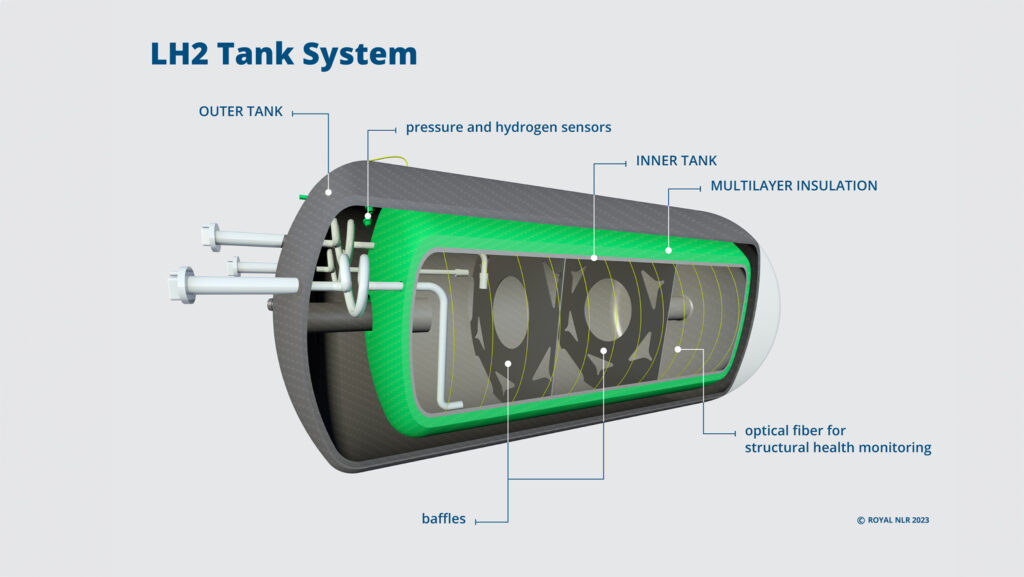
Project partners:
Research organisations : NLR, SAM|XL
Industry (NL) : Toray (project lead), ADSE, Airborne, Bold Findings, Cryoworld, Fokker Aerostructures, IT’S Engineering, KVE, PhotonFirst, Somni Solutions, TANIQ
Universities : TU Delft
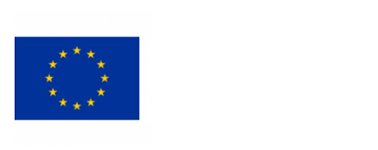
This project is partially funded by the Dutch Government (RVO/Netherlands Enterprise Agency) through “Subsidieregeling R&D Mobiliteitssectoren” (RDM).