Wind tunnel modelling for Europe’s development of the sixth generation launcher
The challenge
The overall objective of the development of the Ariane 6 launcher is to create a reliable, flexible and competitive European launch system.
Flexibility comes in the form of a launch configuration adjustable for smaller or larger payload or lower or higher delivery orbits. The competitiveness comes from the fact that Ariane 6, compared to Ariane 5, can be launched more often per year and cheaper.
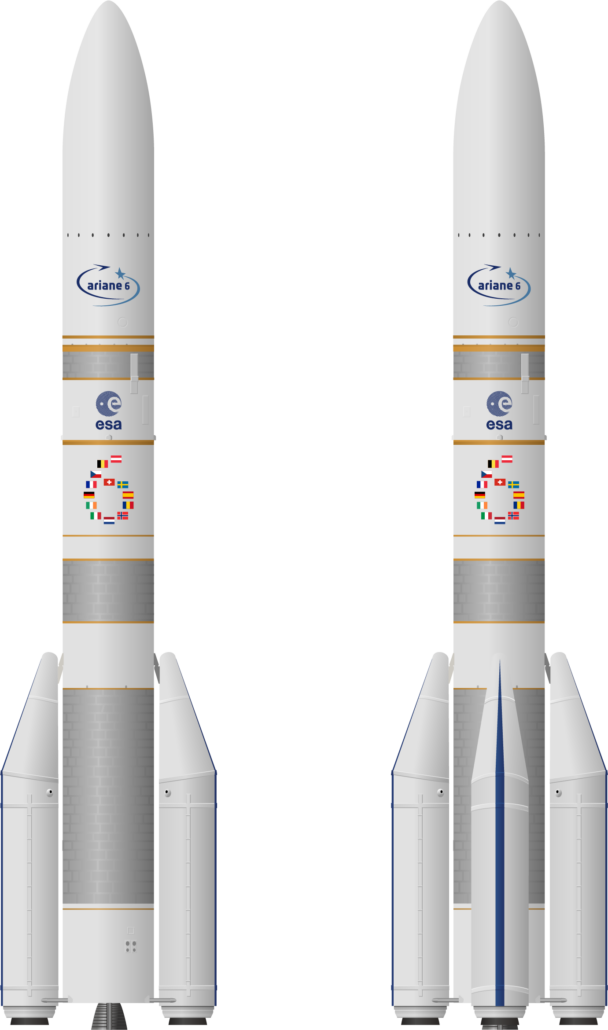
The solution
In the entire development of the Ariane 6 launcher, NLR plays various roles. Most effort of NLR up to now has been devoted to providing ArianeGroup with wind tunnel models for various stages in the development:
- Aerodynamic characteristics of basic lay-out
- Buffeting and acoustic characteristics of detailed aerodynamic shape
- Aerodynamic characteristics of detailed aerodynamic shape
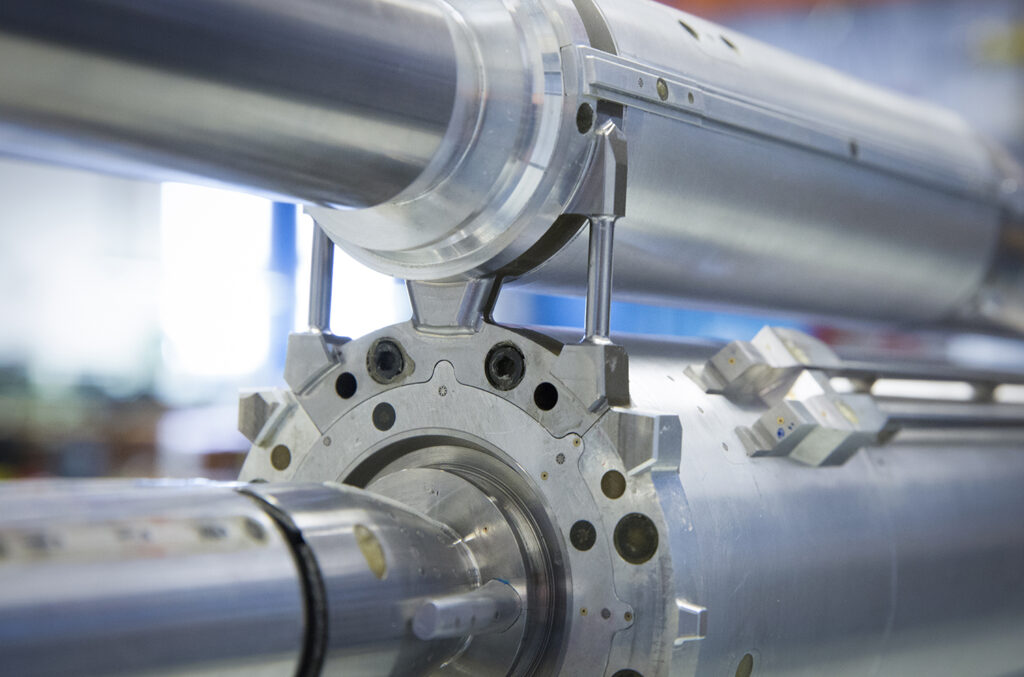
What did we do?
Results from wind tunnel tests performed on the models provided by NLR have delivered the design teams of ArianeGroup valuable data to be able to advance the design. This contributes to realizing the goals of the Ariane 6 project: a reliable, flexible and competitive launcher.
NLR has used its expertise to equip the three models with a significant amount of sensors, be it static or reference dynamic pressure sensors. The available space in the models was minimal which forced the design and instrumentation of the models to be optimized. Modularity of instrumented boosters added complexity but surely also functionality for ArianeGroup.
Project partners:
Industry (NL) : ArianeGroup
Research organisations : NLR, DNW, ONERA
Start : 2014
Duration : 6 years