The design of the PAL-V Liberty rotor blades was undertaken by NLR. Its extensive experience in aerospace engineering and composite structures has been crucial in refining the design and ensuring it meets the high standards of performance and safety. The rotor blades are 20% more efficient with less drag compared to equivalent blades, resulting in better performance and fuel economy. Due to the advanced composite technology used, a set of two rotor blades together weighs only 35.8 kg, despite spanning almost 11 meters in length.
PAL-V and NLR have worked closely together to perfect the rotor blades, leading to the current phase where they are ready for mass production. PAL-V has already set up a small-scale assembly location near its headquarters in the Netherlands, where it is preparing for the serial production of the Liberty flying car.
“We are thrilled to have reached another milestone with our new technology for high-end composite rotor blades,” said Henri de Vries, Senior Scientist at NLR. “Together with PAL-V, we’ve overcome technical challenges and ensured our rotor blades are ready for industrial production. For a gyroplane, the rotor blades will be put in motion by the airflow instead of by a motor. This is called autorotation, which creates lift. So, the PAL-V blades are basically its wings during flight and, next to being light, they contain a mid-hinge to be able to fold the blades to enable driving on the road with a convenient vehicle-length of just four meters. This makes its design unique and unprecedented.”
NLR’s state-of-the-art facilities, including wind tunnels, composite manufacturing facilities, structure testing equipment, and even a landing strip, have all been used in the R&D and certification testing of various parts and subsystems of the PAL-V Liberty. The partnership with NLR will continue to play a key role as PAL-V approaches the launch of its first production units.
“Since its existence PAL-V has been the front-runner in the upcoming advanced air mobility market (AAM), outpacing any player in the market due to its focus on using existing regulations. With the support of numerous suppliers and esteemed partners like NLR, PAL-V now concentrates on finalizing the last stage of air certification and compliance demonstration. With an orderbook filling the first three years of production by a majority of professional customers, as well as private individuals, the PAL-V Liberty will be used to overcome the growing global mobility challenges,” says Robert Dingemanse, CEO and Founder of PAL-V.
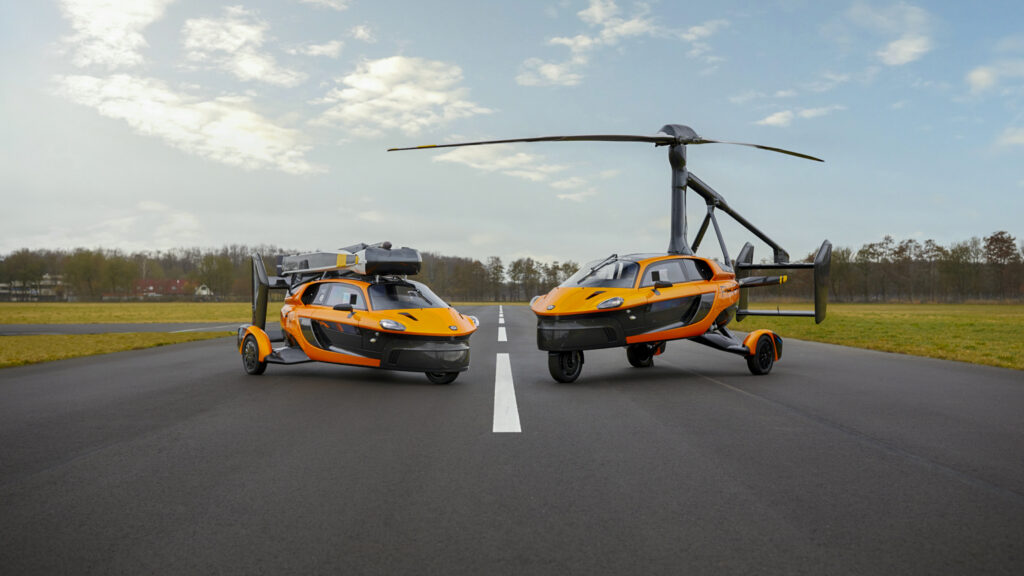