FLAPsense project: optical sensor system for real- time proprotor FLAPping angle monitoring
The real-time monitoring of the flapping of the rotor hub of a Next Generation Civil Tilt Rotor (NextGenCTR) aircraft enables the enhancement of the proprotor performance and operational safety. Accurate deformation and motion measurements in the rotating frame are a highly challenging task. Classic sensors have the drawback that they are highly sensitive to the type and location of installation as well as environmental conditions. Therefore, an optical, non-contact measurement system for real time monitoring of the proprotor flapping angle was developed, designed and manufactured within FLAPsense.
The challenge
The objective was to design and manufacture a contactless measurement system for real-time monitoring of the proprotor flapping angle, which co-rotates with the NextGenCTR’s rotor. This system utilises a highly accurate optical sensing method to provide the avionic system with precise data on the actual flap motion of the rotor blade. Ultimately, the FLAPsense system will undergo flight testing on the NextGenCTR Demonstrator aircraft.
The solution
A bespoke sensor was developed, with the following key characteristics:
- Voltage supply: 28 VDC
- Power consumption: less than 100 W per rotor
- Accuracy: 0.5 degrees
- Weight: less than 0.5 kg per rotor
- Sampling rate: 24 measurements per rotor revolution
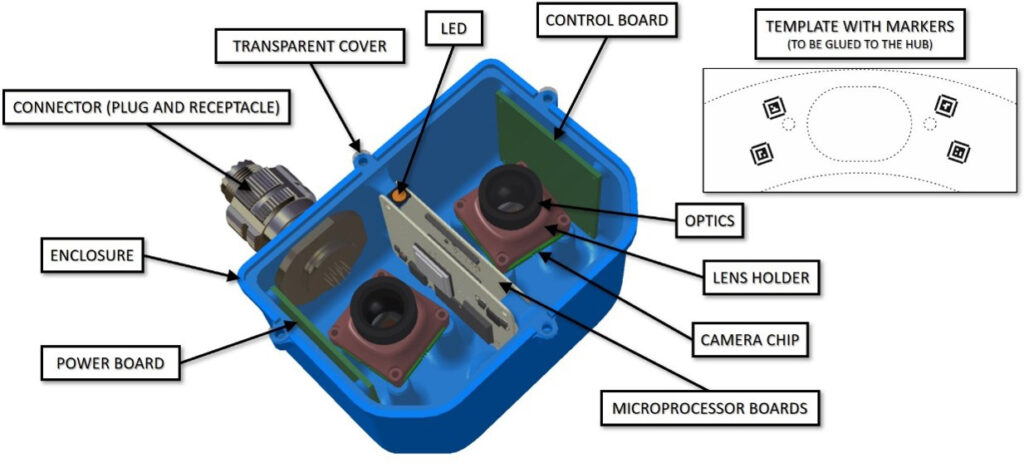
What did we do?
The research conducted by NLR on the sensor system involved defining the interfaces between the aircraft and sensor, and the sensor and Flight Test Instrumentation to ensure seamless communication and data exchange between components.
The work by NLR also included compliance verification and building a rotating test bench to validate the sensor’s performance in a realistic environment.
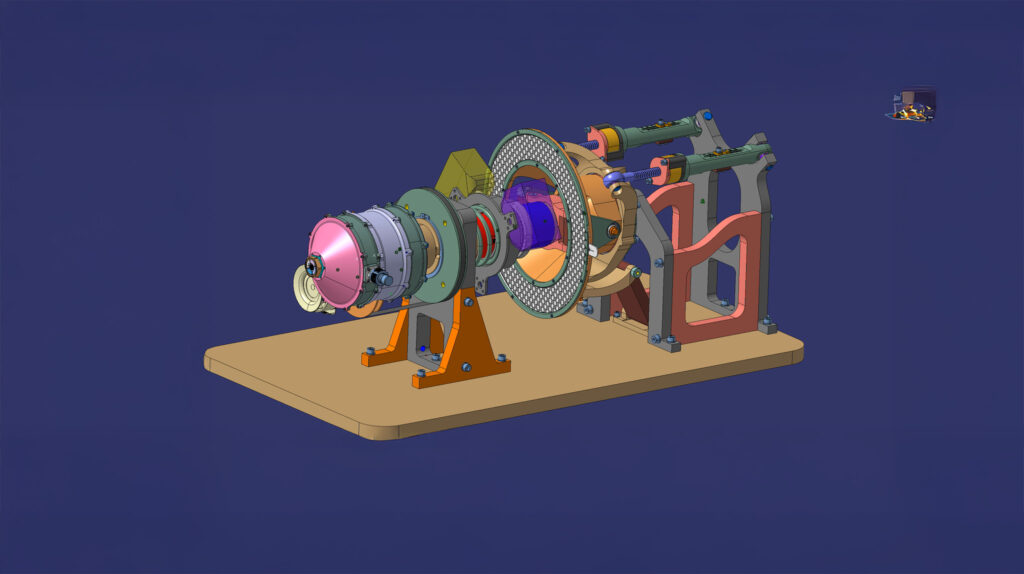
Project partners:
DLR (coordinator), NLR (partner), HIT09 (partner), Leonardo Helicopters (topic leader)
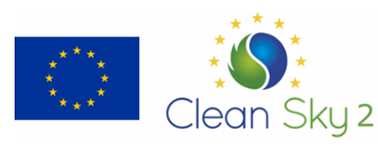
Clean Sky 2 FRC GA no 785571