The manufacturing of complex-shaped composites is becoming increasingly common, driving up demand for fast automated quality control. Laser ultrasonic testing can be a viable technique to achieve this, as it is fast and contactless. However, it requires the inspected part to be perpendicular to the laser beam, posing a challenge for the positioning of the laser or part. Combining laser ultrasonics with optical 3D scanning can overcome this challenge and realise a fast automated quality assurance system for composite manufacturing.
The challenge
To establish an automated quality control system, several challenges must be addressed:
- The system must be able to identify the part area that is perpendicular to the laser.
- The system needs to be capable of moving the part in order to scan the entire component.
- The scan results have to be accurately registered onto a digital mesh.
The solution
We developed an automated inspection system by combining a 3D scanner and laser ultrasonic scanner. First, the 3D scanner creates a mesh of the entire component, providing comprehensive shape information. The shape information is then used to control the rotation table, allowing the laser ultrasonic scanner to inspect the component from all required angles. The system subsequently combines the partial scans that meet the perpendicularity requirement and maps them onto the mesh in order to complete the automated inspection.
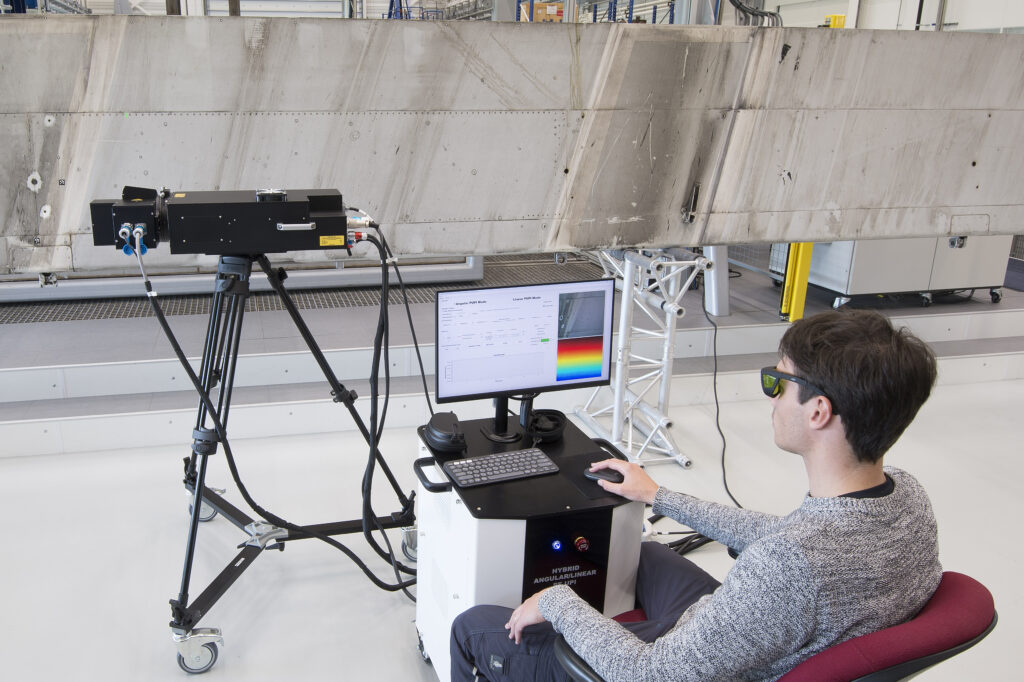
What did we do?
In this project, NLR has combined its expertise in non-destructive testing and structured light scanning to create a fast and automated inspection system. This system enables the inspection of 2D curved composites with the push of a button,
significantly reducing inspection time per component compared to conventional ultrasonic testing methods. Moreover, the method is contactless and allows for fast prototype inspection without requiring prior dimension information.
Project partners:
NLR
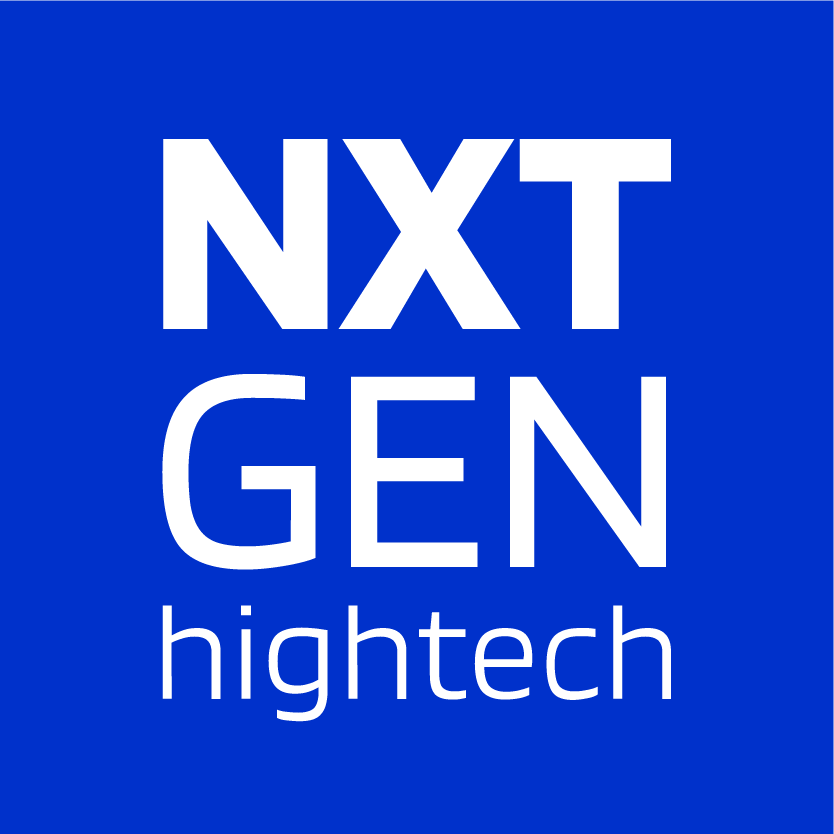
Acknowledgement: This project is made possible
in part by a contribution from the National Growth
Fund program NXTGEN HIGHTECH