This research project aimed to develop additively manufactured propellant tanks using non-standard metals for use in ESPA and ESPA Grande-class satellites. The propulsion systems of Dawn Aerospace use self-pressurizing propellants, eliminating the need for helium pressurants and propellant management devices. This allows for flexible, custom tank designs without additional systems, making Dawn’s propulsion systems simpler, faster to manufacture, and more cost-effective. This flexibility enables Dawn to accommodate various customer needs. The project contributes to the objectives of the Dutch space policy in the NSO roadmap for satellite systems and aligns with ESA’s goals.
The challenge
The goal of this project was to develop titanium propellant tanks for medium-sized satellites using metal Additive Manufacturing (AM). This development is important to prepare for a potential ban on hydrazine. Therefore, the project focused on using industrially available fuels with low toxicity. An additional goal is weight reduction.
The solution
Test specimen and titantium qualification tanks were produced. These test articles have been tested to qualification levels for representative pressures and vibration loads. All test results showed no anomaly. Furthermore, no compatibility issues with the propellants were found.
What we are doing
The compatibility with propellants was investigated through various tests on additively manufactured samples. Tensile testing was conducted to establish design values. The material’s performance was evaluated in different directions and after immersion in the propellant. Leak before burst testing was carried out on flat samples with printed surface cracks. The material had to show pressure relieving leakage rather than unstable crack growth.
Pressure testing, including proof pressure, cyclic pressure, and burst pressure testing, was also carried out. Qualification testing on a shaker with sinusoidal and random vibrations was performed on pressurised tanks to assess their performance under operating conditions, ensuring reliable operation.
Project partners:
Dawn Aerospace (lead), Royal NLR, TNO-Energetic Materials
Period: 2021 – 2023
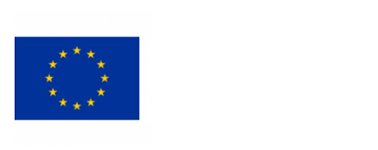
Funded by the Netherlands Space Office (NSO): Small Business Innovation Research (SBIR)