Digital twins improve control the production process and help optimise it. The digital variant goes through the same process steps at the same time as its real-world counterpart. This ‘image’ is offering more and more possibilities. Senior scientist Erik Baalbergen, who has been involved in developing this technology for several years, explains what it means for NLR.
“We want to get a clearer picture of the application of innovative supporting technologies in aerospace development and manufacturing so that production can become more efficient and greener. As part of that, we’re investigating how humans and systems work together. Modern automation and the presence of increasing numbers of sensors give us access to a great deal of data. This innovation gives us new understandings during the production of composite parts and helps us optimise the production processes. We set up a test environment for this a couple of years ago at NLR in Noordoostpolder, together with Fokker Landing Gear.”
“We want to help the operators, for instance,” explains Baalbergen. “This pilot plant includes an RTM machine – that stands for ‘Resin Transfer Moulding – for resin injection. Once you’ve produced a semi-finished item, you need to inject it with resin. The RTM is in fact an aggregation of several machines, with not only the resin injector but also a number of water heaters to keep the resin hot as it travels to the mould. That’s a pretty complex setup and the operator needs to be there at all times to keep an eye on everything.”
NLR is working from the operator’s role as the starting point for these latest developments in digital support for production processes. According to Baalbergen, the challenge is linking OT (Operational Technology) intelligently to IT applications.
“This is a pretty heavyweight industrial automation job for the machine setup and we’ve adopted the concept of the ‘digital twin’ as a computerised copy of the RTM process.”
Help for the operator
Using the digital simulacrum has a clear, predefined goal.
“Ultimately, this digital twin has got to help the operators,” says Baalbergen, “so that they don’t have to respond to all kinds of alarm bells so often. The digital twin has to keep an eye on all the details constantly. The operator can then pay full attention to certain specific phases of the resin injection process where just the right touch is needed for responding appropriately if the situation so demands. To that end, you have to run simulations as well and carry out data analyses. The ultimate aim is at a higher level: we want to have the whole pilot plant run by a single operator. That will mean not only automating a lot more aspects but also responding to incidents more intelligently. You’ve got to avoid having too many false alarms, so you only want the essential ones to alert the operator.”
NLR will have to resolve a variety of problems to do this, in part because the rules for the aviation industry are strict. “All the processes are certified,” says Baalbergen, “so we’ve got to be careful not to ‘leave it to the computer’ too much. To give you an idea, suppose that the mould temperature has to be eighty degrees and the alarm has to sound at eighty-two. The standard response is that the operator turns the temperature setting down if the alarm goes off. That would be simple to automate, but that’s not allowed. The process has got to be assessed by an operator. So a lot of conditions like that need to be applied. Within those limits, we’re aiming to automate as much as possible and assist the operator.”
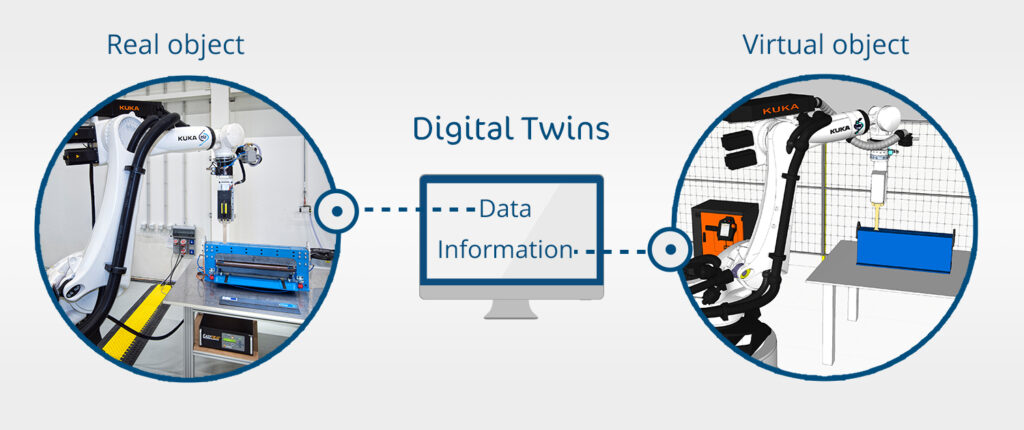
Further development
Following on from the development of a digital twin, Royal NLR is working with an aircraft manufacturer, a technical college and an equipment supplier in a project called Luxovius, in which a digital twin will be created for an innovative production process.
“Lots more sensors are needed in and around the machines for it,” says Baalbergen, “because you want to use as much data as possible to get a good digital twin. In the end, we want this project to give us a production process that’s as efficient and as ‘green’ as possible, consuming the least possible amount of energy and generating the minimum possible amount of waste.”
The operator’s role will not be superseded by these technological developments, he says.
“You’re not going to phase the operators out; instead, you’ll be deploying them for things they’re better at, with more scope for their own creativity. We’ve interviewed operators and explained the benefits of digital twin technology to them, and they’re enthusiastic about it too. You’re helping them to cut down on the boring administrative aspects of the job. So you’ve got to explain the potential of the new technology properly. At the same time, we want to make sure that digitising complex processes and systems doesn’t force people to adapt to the computer. Get that computer to adapt to the people! That lets you work much more efficiently. Digital twin technology simply makes it easier for the end user, so that operators can make better use of their own creativity.”
This article is a translation of an adapted version (made with the agreement of the author, Dimitri Reijerman) of an original text on the website of the sector association FHI for the Machinebouwevent of 1-3 December 2020.
Want to know more?
Royal NLR has a research platform (manufacturing machine, real aircraft and/or simulation environment) to investigate Digital Twin and Industry 4.0 opportunities. Read more about NLR’s Digital Twins capability