On-board computers allow sophisticated processing of the large amounts of data received from increasing numbers of miniaturized high-resolution sensors located in small satellites. “Their electronics produce heat that needs to be dumped into space,” explains Johannes van Es, principal scientist of the Thermal Control Group at NLR. “This prevents functional failure or even worse.”
At present, thermal issues for CubeSats and small satellites (<100 kg) are resolved using passive means. But as satellites evolve, it is assumed that thermal problems can arise at anywhere above 20 watts. “The power increase requires a more advanced thermal control system (TCS) to let the CubeSats operate in a hostile environment with no air, large temperature fluctuations and zero gravity”, according to Johannes.
Their electronics produce heat that needs to be dumped into space
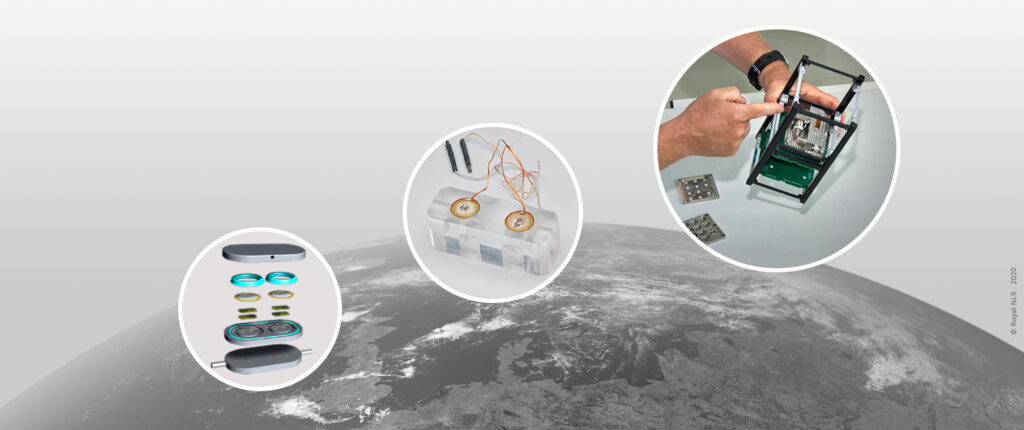
Mechanically pumped Loop
To integrate a TCS into a CubeSat, it needs to be low-cost, physically small, low in power consumption and both modular and flexible. As a robust solution for this, Royal NLR developed a new thermal concept, the mini mechanically pumped loop (MPL). It transports the heat dissipated at hot spots to thermal radiators where the heat is radiated away into space. The heart of the system is the multi-parallel micro-pump (MPMP), which provides a low-mass MPL solution with high reliability due to multiple pumps in parallel for generating the flow. This design avoids the single point of failure of one pump in the loop. The individual micro-pumps are piezo-driven displacement pumps with passive micro-valves. The flat design allows similar performance both on the ground and in micro-g operations in space.
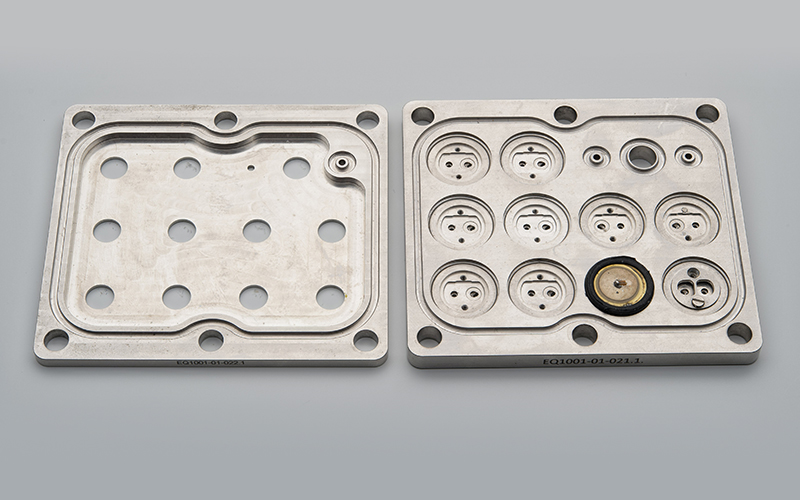
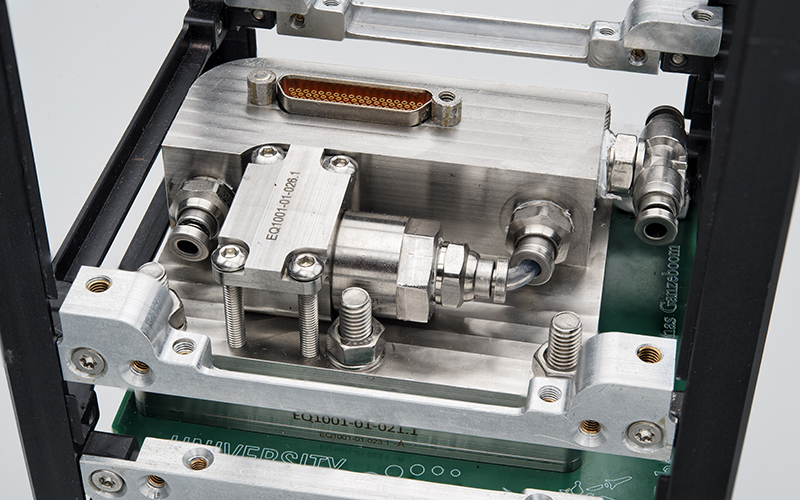
CubeSat modular thermal modelling
The absence of thermal control solutions for current CubeSats is inherently related to their short development times, which have resulted in suboptimal thermal designs. Increases in power density mean that thermal control measures are needed, requiring low-cost hardware and software solutions. Together with the CubeSat manufacturer ISIS (Innovative Solutions in Space), NLR developed an innovative modular approach for CubeSat thermal analyses using ESATAN-TMS.
The key to this approach is the interchangeability and scalability of validated thermal submodels allowing fast and more accurate analysis for low Earth orbit (LEO) missions. Any design can be quickly evaluated in ESATAN-TMS in the CubeSat frame model. Eventually the thermal model can describe the advantages and drawbacks of the system compared to conventional thermal design options.
Cooperation
The conventional space industry and institutes have built up experience over time with TCS, modelling and testing the systems for larger satellites. However, the conventional approach does not suit CubeSat development. Combining the test methodologies developed by NLR and lessons learned with the knowledge and knowhow of CubeSat system engineers has brought together best of both worlds. The combined efforts of NLR, ISIS and the University of Twente have linked knowledge of thermal systems, experience in thermal modelling and testing plus low-cost tool availability together effectively.
What are CubeSats?
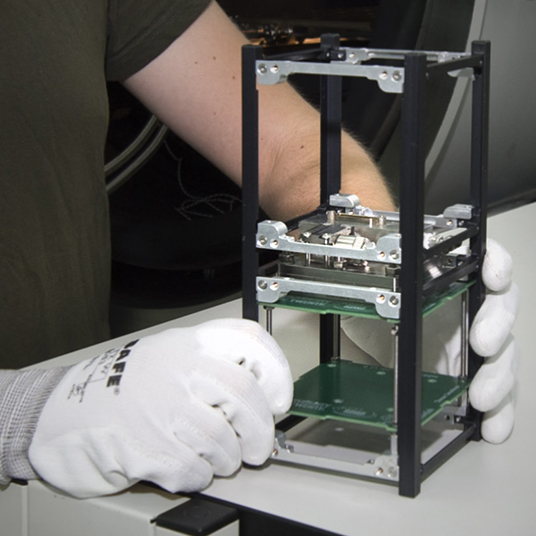
The sizes of small satellites (also known as nanosatellites) follow the CubeSat standard, which defines the outer dimensions of the satellite within multiple cubical units (U). 1U is equivalent to dimensions of 10x10x10 cm. A typical size that can accommodate small technology payloads is a 3-unit CubeSat with dimensions of 10x10x30 cm. A TCS becomes relevant for 3U CubeSats with large deployable solar panels or 8U without deployable solar panels.
ESATAN-TMS
Read more
of the report about the mini mechanically pumped loop for CubeSat thermal control: the mini Mechanically Pumped Loop for CubeSat thermal control written by NLR together with University of Twente and ISIS (Innovative Solutions In Space).
about thermal modelling using in ESATAN-TMS: written by NLR together with ISIS (Innovative Solutions In Space).
The ESA Thermal Analysis Network (ESATAN) software was first made available to users in 1985. It is now the accepted standard space thermal analysis tool for ESA projects.
Any CubeSat design can be quickly evaluated in ESATAN’s Thermal Modelling Suite (TMS) by implementing a combination of validated thermal submodels in the CubeSat frame model. A library of validated thermal submodels will be created over time in ESATAN-TMS, allowing fast and accurate orbital analysis, which results in improved thermal designs for CubeSats.
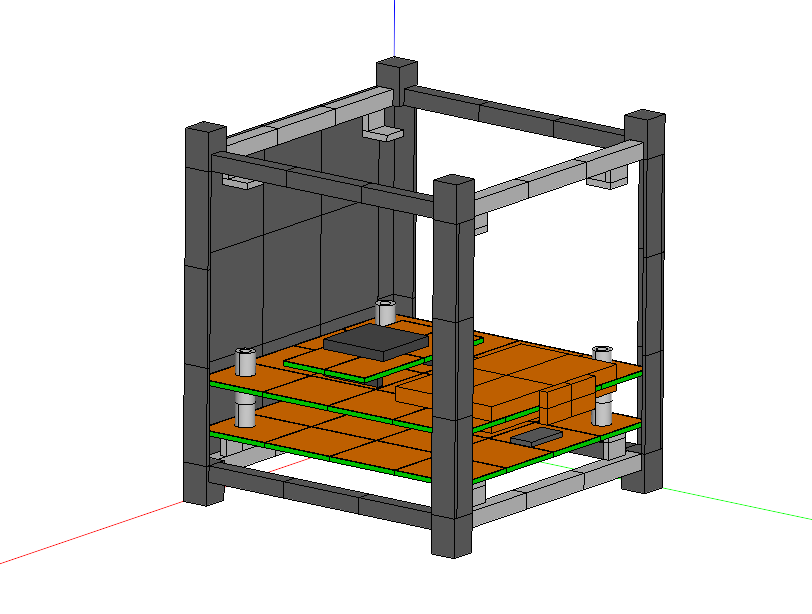