NSO, the Netherlands Space Office, has awarded Dawn Aerospace a €500k Small Business Innovation Research (SBIR) Phase Two grant.
Funding will support research on additively manufacturing propellant tanks using non-standard metals for use in ESPA and ESPA Grande-class satellites. Research partners include TNO – Energetic Materials, and Royal NLR – the Netherlands Aerospace Centre.
Dawn satellite propulsion systems use the self-pressurizing propellants nitrous oxide and propene. They do not require helium pressurants or propellant management devices as is common with standard space propellants like hydrazine. This is important because it means Dawn can additively manufacture propellant tanks in a wide range of form factors, specific to each customer’s satellite without the need for custom propellant management systems. This makes Dawn propulsion systems simpler, flexible in design, faster to manufacture, and cheaper.
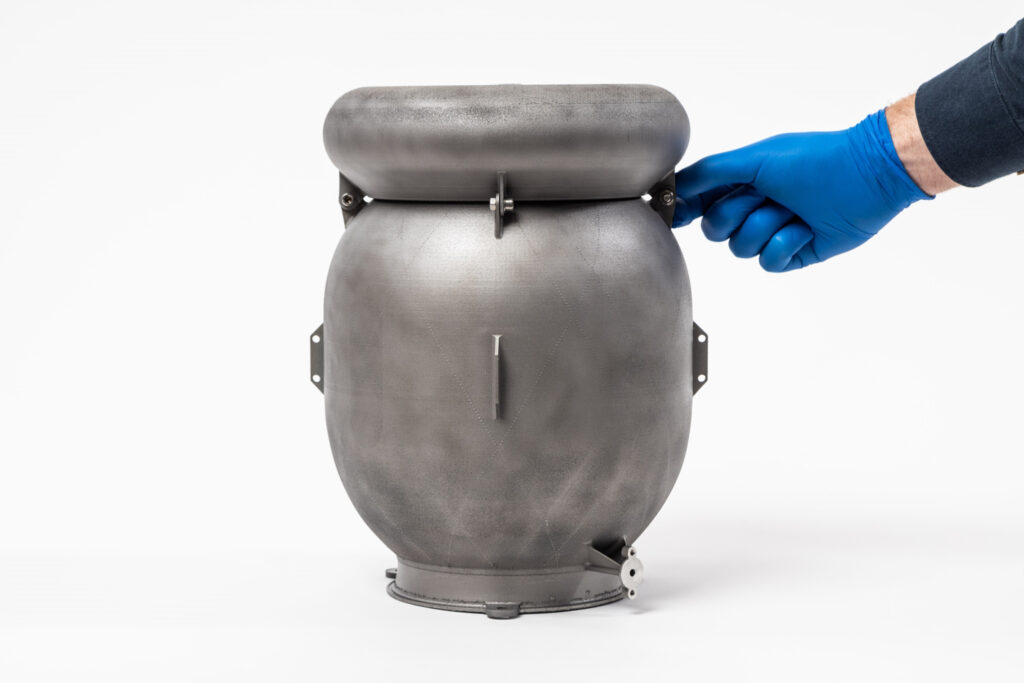
“We can make tanks to suit nearly any satellite form factor, and we’re already using additive manufacturing to do this,” states Jeroen Wink, Dawn co-founder and CRO. “However, the stranger the form factor, the higher the mass penalty. Through this NSO-funded research, we hope to remove these mass penalties and give our customers complete design flexibility.” Compared to the main European alternative for ‘green’ satellite propulsion, LMP-103S (ADN), which uses the classic blow-down pressurization architecture, Dawn’s system impulse density is more than 50% higher in many cases. “We hope to reduce our tank mass by a further 50%,” states Wink. “That will result in even more system impulse density, delta-v and performance for our clients.”
“NLR is excited to contribute to the project with its unique metal additive manufacturing knowledge and facilities such as the NLR Metal Additive Manufacturing Technology Centre (MAMTeC). This will stimulate future production of qualifiable propulsion components for space application by additive manufacturing in the Netherlands”, says Marc de Smit, R&D Engineer at NLR.
Dawn was one of ten companies to receive Phase 1 funding earlier this year for feasibility studies. The five most promising innovations received further funding — €2.5M in total. This is the first time SBIR funding has been made available to develop aerospace hardware. It’s part of a strategic call by the Netherlands government in “Technology development for space infrastructure,” advancing Netherlands-based offerings for future European Space Agency and commercial missions.
“The aim of the SBIR is challenging companies from the Netherlands to show their technological and innovative capabilities”, says Ramon Peeters, Project Leader of the SBIR-T at NSO. The products must contribute to the ESA programs and thus to the information needs of the Dutch government in the long term. “Those who are able to show a proper prototype will make a better chance at tenders for future space missions.”
See our website for additional information about additive manufacturing: https://www.nlr.org/capabilities/additive-manufacturing/