As much as we thank the pilot for a successful landing, the real main protagonist of the landing gets little credit: the landing gear. The landing gear is a complicated piece of advanced technology, but it is also a bit of old-timer in terms of usage, when compared to other, even less vital, parts of an aircraft. Landing gears are designed based on a sort of “single use” concept, called “safe-life”; this means that after a specified pre-determined number of landings, the landing gear is removed from the aircraft and disposed. This also means that landing gears are manufactured to be used only within strictly defined boundaries. Following any kind of incident or use outside those boundaries, differently than other parts of an aircraft, landing gears are not repaired, they are simply replaced. With a significant impact, on the availability of the aircraft and on the economic side. In addition to this, it is not always easy or possible to detect if damage has actually occurred, which pushes more operators towards the safest decision of replacing the landing gear when in doubt.
To help changing the way the landing gear is utilized and managed in real-life situations, thus leading to a new paradigm in aircraft availability and operability, Meggitt, Technobis, Airbus and NLR came together in project ALGesMo.
Get to know your landing gear
Frank Grooteman, senior scientist at NLR and NLR project lead, explains: “Currently it is not possible to have any information about the status of the landing gear, about the loads acting on it or the occurrence of overloads. Several systems have been tried in the past to measure the loads on a landing gear. These all failed for one reason or another.”
Within the ALGeSMo project a system that measures the loads on the landing gears and provides load data to various aircraft systems has been developed. The data collected is expected to be used for structural health monitoring, hard landing detection, weight and balance and flight controls, and could be extrapolated to various other possible checks. The system considers a new, very promising approach, based on the use of optical fibre Bragg grating (FBG) sensors. These sensors consist of a small grid inscribed in a standard telecom fiber that can measure the strain or temperature and offer several advantages over traditional sensors, such as low weight, no electromagnetic interference, no need for recalibration and robust for harsh environments.
In the ALGesMo project, a complete monitoring system has been developed and tested on ground. The whole system has been thoroughly tested in a dedicated test rig at NLR to determine its performance under realistic limit load conditions and endurance testing at low and elevated temperatures.
Beyond expectations results and next generation aircraft
Frank Grooteman reports on the results achieved during the project: “ALGesMo achieved results beyond the expectations of the project team. The system developed does not only measure the vertical loads on the landing gears, like the previously fielded systems. It measures the loads along all three axis and the braking torque about the wheel axles of the main landing gear. It therefore allows more benefits that previous systems, beyond the weight and balance measurement, by detecting overloads and providing real-time brake control”.
Thanks to the accurate load monitoring, design and weight optimisation of the landing gear can be proposed; next to this, an on-condition maintenance schedule, based on current health monitoring data, could be implemented, reducing down-time of the aircraft and improving its availability for the airline.
Embedding of sensors in composite materials exposed to high temperature conditions was also a challenge, as such environment can cause non-uniform mechanical strain on the optical fibre during the curing process. A suitable combination of epoxy and fibres for the composite had been identified by Meggitt together with process parameters which eliminate the problem.
Other beyond-state-of-the-art advancements have been achieved in the avionics needed for recording the measurements. A fully integrated avionic unit containing the optical interrogator, based on the latest optical chip technology, together with processing and communication electronics, has been developed by Meggitt and Technobis (PhotonFirst) and was named Fibre Optic Processing Unit (FOPU), allowing the system to have a small and robust interrogator, and novel product. The connector between FOPU and its rack were also more challenging than on existing systems, given the need to transfer optical signals, which are more sensitive to perturbations and power loss, especially in challenging environments with varying temperatures and vibrations. A solution, that went beyond the previous state of the art, has been developed thanks to a fruitful collaboration with a connector supplier, which led to the development of a new reliable and robust connection for this type of environment.
The results achieved in the project are seen as promising by Airbus, who seeks to incorporate the developed system in a production system to be fitted on a future Airbus aircraft.
This project has received funding from the Clean Sky 2 Joint Undertaking (JU) research and innovation programme
under grant agreement No 717179.
The project was also supported by the Swiss State Secretariat for Education, Research and Innovation (SERI) which was partially funding the project activities under the responsibility of the Meggitt Swiss entity.
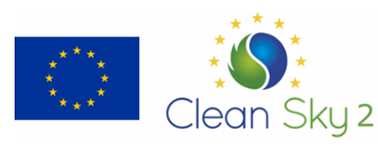