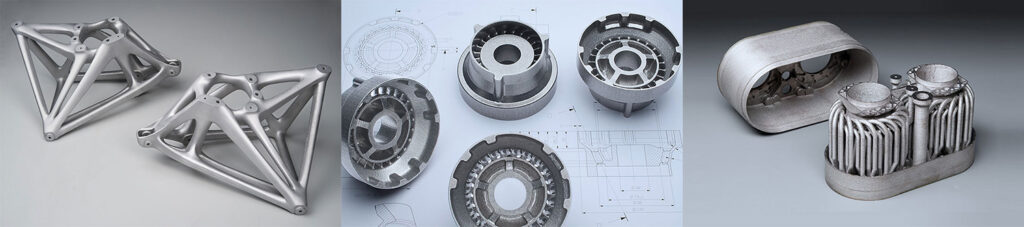
“In the first programme, we have only used laser powder bed fusion. In the new programme, we are also going to work with another additive manufacturing process,” says Marc de Smit, R&D engineer at Royal NLR. “Now we are going to work with blown powder directed energy deposition too, a process in which the metal powder flows out of a nozzle and is then melted immediately with a laser. It is a process that is suitable for making large components, adding components to existing products or carrying out repairs.”
Before we delve into how the technology works, let’s start with some history. “The hype around metal printing reached its peak in 2014: expectations were high and everyone is very interested was very interested,” says De Smit. “Metal additive manufacturing offers lots of opportunities, including the possibility of making products that are lighter, made from fewer components and that perform better. This technology offers possibilities for making aircraft more lightweight and therefore more economical and more sustainable. Lots of applications can be thought up in other markets where the freedom in design offered by metal additive manufacturing can yield substantial benefits. NLR has already worked on a number of applications. Hydraulic systems can be optimised so that the resistance to the fluid flows is less; more lightweight and more efficient heat exchangers can be produced and structural brackets can be optimised in such a way that the weight is substantially reduced.”
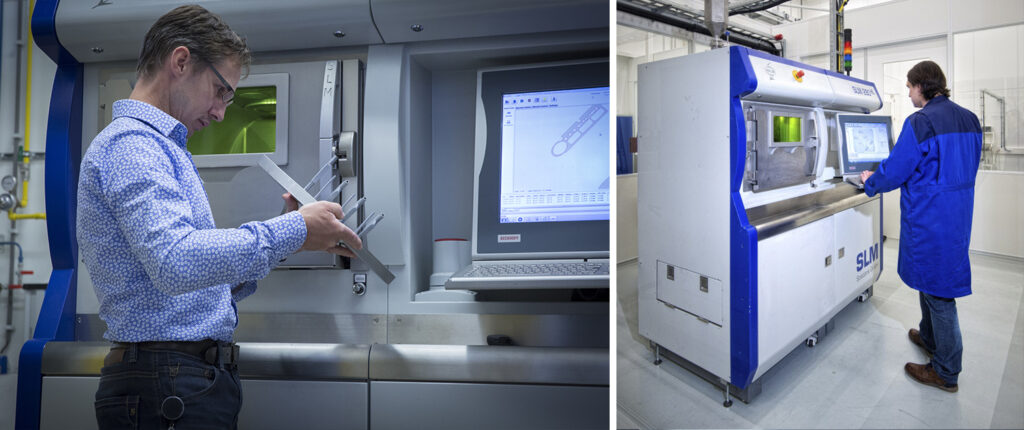
One problem with the new technology is that a great deal of knowledge is required if genuinely good, safe products are to be delivered. This refers not only to the product design but also to knowledge about the basic materials, the process, the material properties and (last but not least) the requirements if the product is to be certified.
The content of this cooperative project is based on the requirements of the companies that are interested. Important topics are (for example) process optimisation so that good materials can be made, determining the physical strength of the printed material produced, further processing of the printed products and the designs for additive manufacturing so that the maximum benefit can be achieved. The technology demonstrators provided by various companies have been optimised and developed within the programme.
High demand for knowledge
De Smit explains that there was a high demand in the early days for knowledge relating to all aspects of metal additive manufacturing, such as questions about design rules, the process, heat treatments and post-processing. Such knowledge was only available to a very limited extent in the Netherlands when the first programme started. “The process for melting powder particles together with lasers needs a lot a different settings to be combined,” says De Smit. “Take for instance variables such as the laser power, the speed, the distance between the laser scan lines, the powder layer thickness, and lots more. Different parameters have to be used for each material. One of the aims was to come up with an efficient method for quickly selecting the right settings, and we managed to do that.”
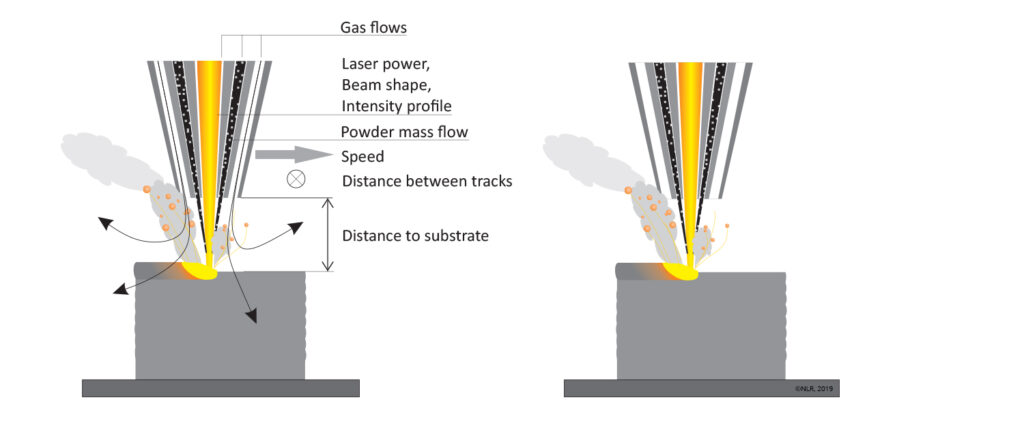
Design optimisation
One of the major advantages of metal additive manufacturing is the huge amount of design freedom. This process makes it possible to design products that are lighter and that perform better than products made by conventional methods. The example that De Smit gives is a T-piece for a hydraulic system that reduces the flow resistance. “Removing material where you don’t need it makes the design lighter and the improved internal shape means that there is less resistance to the fluid flow inside the manifold. An additional benefit is that the lower flow resistance means that a lighter pump can be applied.”
Certification
If the printed components are ultimately to be used in highly demanding applications, certification of the 3D-printed items is essential. The requisite procedures for this have not yet been developed, which is why that objective is one of the key elements of the new programme.
“The most difficult aspect is being able to prove that you do know exactly what you’re doing,” says De Smit. “You have to be able to demonstrate that there are no flaws in the materials that could result in a product failing. You could do that with a CT scan, for example, but that’s time-consuming and expensive because every component has to be scanned. It is therefore very beneficial if detailed process monitoring is developed that enables detection of when material defects are created.”
De Smit also explains that monitoring the processes is not only about the direct knowledge of the materials and the process, but also about processing large quantities of data. “Monitoring systems are used to watch what is going on in the melt pool. A lot of information is generated during the production process. All that data ought to help us determine whether the process went well or not. In the future, we would also like to add artificial intelligence to the processes, for example so that any flaws that are detected can be repaired.”
Technology demonstrators
All those work packages came together in what is referred to as the ‘technology demonstrators’ package. The companies taking part were given the opportunity to include their own technology demonstrator in the programme. The individual requirements of the various partners are extremely important because each type of industry imposes different requirements and has other objectives.
De Smit says, “We have designed and produced demonstrators for various partners. A component was made for Mokveld that enables improved separation of water from oil. The Oerlikon demonstrator is a wire erosion tool that was redesigned with topology optimisation. For Fokker Aerostructures we optimised hydraulic manifolds. A substantial weight reduction and pressure drop reduction was obtained. A structural bracket was redesigned for Fokker Services. The weight is substantially reduced while the strength requirements are still met.”
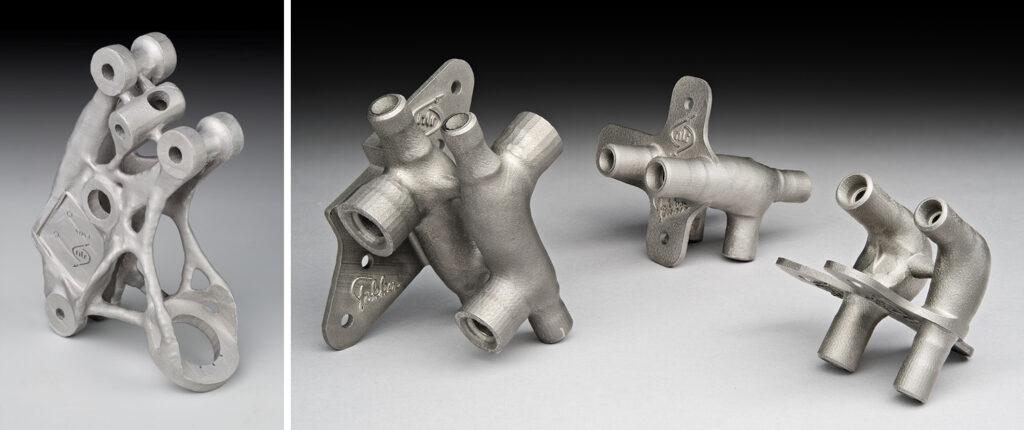
New programme
The new four year programme has started in April 2019 and has been drawn up once again from the wish-lists of participants. The main goal of this new programme is to support the participants in their ambition of introducing certified metal AM components. In numerous sectors, particularly aerospace and high-tech, it is important to demonstrate that the Additive Manufacturing process is reliable and reproducible. Certification of AM components is important to enable safe and sustainable implementation in various demanding applications.